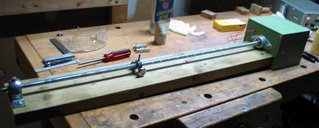
You can click on any picture here to enlarge it.
The DC gearmotor is in the green box to the right. The output shaft of the gearmotor is coupled to the galvanized steel drive screw shaft inside the box. Both ends of the drive screw are supported with pillow block bearings, a flange mounted ball bearing unit (Dayton 4X727) at the motor box and a bronze bearing pillow block (Dayton 2X567) at the far end. That is an ordinary pressure treated 2x6 that forms the support. You can see the yoke assembly in about the middle of the screw. The limit switches haven't been added yet.
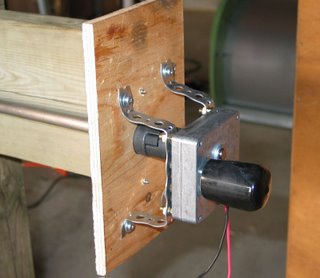
The 1/4" motor shaft is coupled to the 1/2" drive screw with a pair of spider couplers, like Woods L050 series which match the size of the two shafts and provide for a bit of mechanical misalignment if there is any.
I'm not that proud of the motor mounting which is just a pair of galvanized steel perforated strips, shaped to suit the motor distance back from the panel, but I was in a hurry to see it work and this seemed to do the trick. It's stayed that way for the last two years and works to hold the motor securely in place.
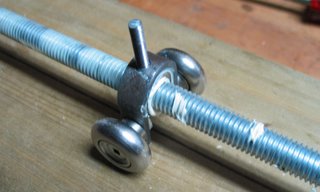
The white goop on the thread and at the nut is white lithium grease. I connected the gearmotor to a DC supply and allowed the motor to turn steadily while I dabbed the white grease in it's path. To the left, you can see the grease spread out on the screw. I ran it back and forth over the whole distance I expected it to travel and kept dabbing grease on it until it was liberally coated smoothly and evenly. After two seasons, there is no rust and no apparent wear to the thread or the nut. I haven't re-applied the grease but probably will this spring.
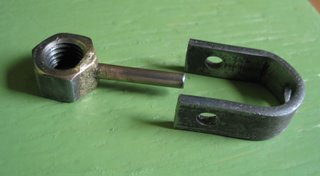

If I was a better welder, I might have brazed this whole assembly. Because of the large area beween the nut and the frame for the glue to grab, I had much better confidence in this approach. I am using an epoxy by Locktite called Hysol 907. It is amazing stuff, but does require suitable curing time (24 hours is recommended for full strength), or a heat cure (150 degrees F for about 2 hours). The surfaces to be glued should be roughed with silicon carbide sandpaper and cleaned with de-greaser prior to gluing.
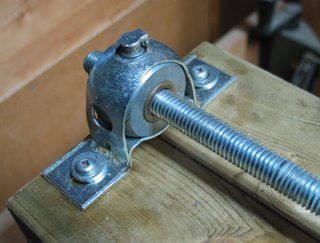
The oil cap is a nice touch and I even put a few drops of oil in it. The protruding oil cap did end up being a bit of a nuisance later as it interfered somewhat with the actuator rod which swings near it on it's way to the drive rod.