
The reflector ends up looking like a shiny inside-out canoe. The parabola is shaped to bounce sunlight onto the pipe which is at it's focus. The pipe also serves as the support for the collector and it's the pivot to allow the heater to follow the sun. The collector pipe doesn't move.
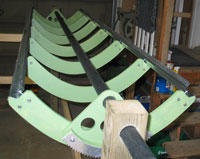
The most expensive, but most impressive, at about $8-12/sq.ft. (German made MIRO IV) is an optically clear anodized aluminum electro-polished material sold by a local distributor in Brampton for use in light fixtures. Curiously, the distributor does not recommend exposure to the elements. We'll see. I've had a sample outside for almost a year now and it seems to be holding out very nicely.
The cost of building only two heaters with MIRO IV is estimated to be about $300 but the cost comes down slightly with larger quantities. MIRO IV is like a metal mirror and the reflection of light in ideal conditions is over 95%. It is an almost perfect mirror that can be bent. One nice feature of MIRO IV is that it is fairly stiff material at about 0.20 inches thickness, so it sits firmly in the frame and is quite strong. My only concern, other than the cost, is the long-term effects of having the aluminum in contact with the galvanized edge of the frame. This will undoubtedly lead to galvanic corrosion at that interface.
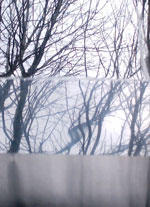
I also tried galvanized steel sheet which I found at the local building center, conveniently cut into 2x8 sheets at only $15 bucks a sheet (about $0.50/sq.ft.!) and learned about the significance of Herscel's infrared experiment in 1800. The galvanized steel showed me that even with a relatively "dull" material that the infrared portion of the sun's energy contained a lot of heat (about half). In a side-by-side comparison, the galvanized sheet contributed about half of the heat energy as did the Anomet material, making it's cost per BTU a lot lower.
The galvanized sheet when new is quite shiny, in a blotchy sort of way. This is the zinc coating that sacrificially corrodes and thereby protects the steel underneath from rusting. You've probably noticed how galvanized metal turns dull and flakes of white oxide form on its surface. Eventually the zinc disappears and the steel rusts. This process depends on the weather and the amount of acid and salt in the air. Just how long reflectors made of galvanized material would be tolerable I don't know. But they do reflect infrared (the visible part of the spectrum is scattered or absorbed). It's interesting that the galvanized material gets quite warm to the touch which wouldn't be the case if it was doing it's job and reflecting all the sunlight onto the collector tube.
One more thing about the galvanized: it is a low cost way to build a prototype that can be later replaced with something better. To replace the sheet in a frame only takes about 10 minutes, so it is easy to upgrade or replace a corroded sheet.
I tried an aluminum sheet product that is sold to the roofing trade for flashing (for about $1-2sq.ft). It is available in standard widths, usually on a roll, at the home centers and comes in various colors including "clear" or natural aluminum. This material in the clear aluminum form produces heating results similar to the galvanized and is a lot thinner, only about 10 thou thick. This makes it slightly harder to handle as it is quite "flippy". You can distort a sheet by mishandling it and produce a crease in the material that ruins the optical properties in that region of the sheet. Also, as the sheet is not anodized like the Anomet and it will degrade more quickly over time like the galvanized sheet. I decided not to use the aluminum further. Although it may make a great prototype material and seems to be readily available in precise and clean 24 inch widths up to 200 feet long.
Any roll material would need to be cut into 8 foot lengths to fit the collector frame. I found it difficult to get clean cuts using tin snips on any of the sheet metal products and I tried to buy them where ever possible in the 2x8 final form.
The winner so far is an acrylic clear plastic mirror material that I only installed about two weeks ago at a cost of about $1.50/sq.ft. This is a 1/16 inch thick version of the plastic mirror used architecturally in public places where they don't want breakable glass mirrors. A local plastics distributor had in stock the 1/4 inch thick acrylic mirror material which I didn't think would bend into the frame easily. They special ordered the 1/16 inch thick version for me.
The acrylic mirror goes into the frames beautifully, although even at 1/16 of an inch it is by far the thickest reflector I've tried. The quality of the reflection and focus is as good, if not better than the Anomet.
The acrylic mirror needs care in handling because it can be broken if bent too far. It becomes strong in the frame but getting it there needs two people.
The long term durability of the plastic is uncertain at this point, but it gives good reflection per dollar and it doesn't get hot in the sun showing that it is doing its job.
I'm not sure about galvanic corrosion where the acrylic mirror (which is probably sputtered aluminum) touches the galvanized frame. We will see with time.
Thanks for your interest.
George Plhak
2 comments:
How has the acrylic mirror material worked out for you? I am working on a parabolic reflector and am seeking optimal materials for the job.
Thanks,
Kevin
Austin, TX
Hello Kevin. The acrylic mirror is holding up very well here, now (Jan 2011) in the third year for the current mirrors. I've written here at the blog about a problem I was having with back illumination causing deterioration and the solution to that problem but now that is solved and the mirrors are proving to be quite durable. I haven't had a serious hail storm yet though and that might be a concern.
Post a Comment